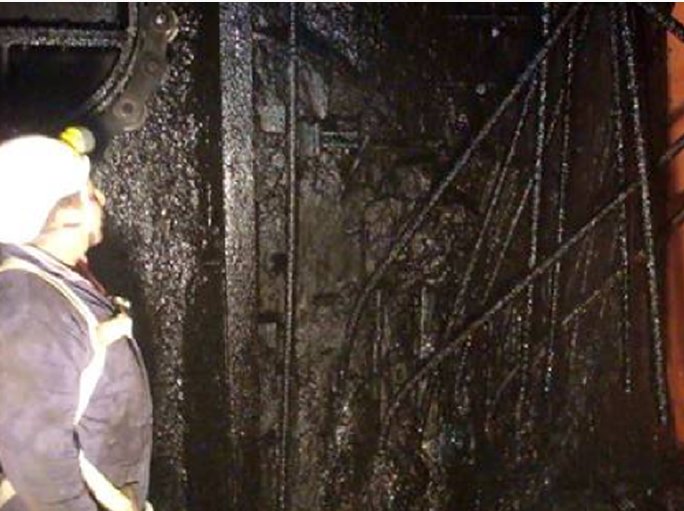
Simón Bolívar Hydroelectric Plant: Repair of the Water Intakes of Units 1, 2, 3, 4 and 9 of the Power House I. Guri. Venezuela, 2008 – 2011.
22 de August de 2011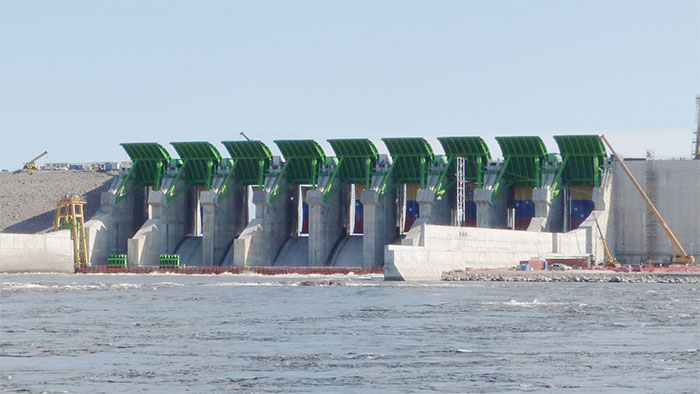
Manuel Carlos Piar Hydroelectric Power Plant: Assembly and installation of the radial gates of the spillway. Tocoma.
26 de July de 2015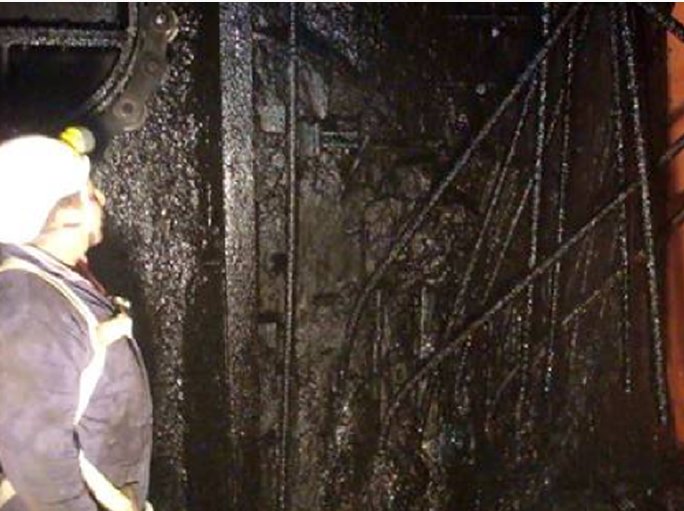
Simón Bolívar Hydroelectric Plant: Repair of the Water Intakes of Units 1, 2, 3, 4 and 9 of the Power House I. Guri. Venezuela, 2008 – 2011.
22 de August de 2011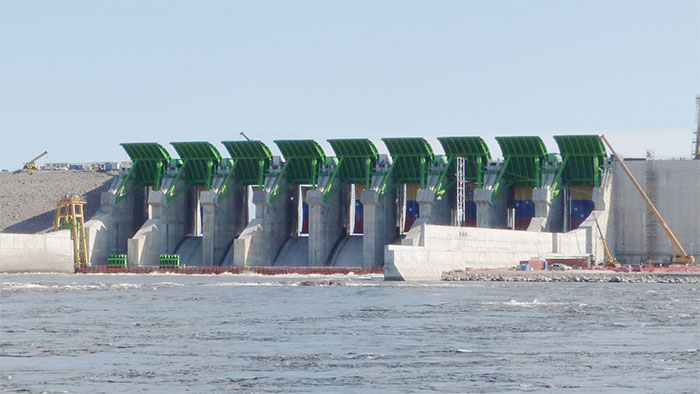
Manuel Carlos Piar Hydroelectric Power Plant: Assembly and installation of the radial gates of the spillway. Tocoma.
26 de July de 2015Simón Bolívar Hydroelectric Plant: CFS, Rehabilitation of the seal frames of the water intakes, Powerhouse No 1, Guri.
The national electricity company CORPOELEC C.A., in charge of operating the national electric supply system, as part of the improvement and modernization of the national electrical system, developed the engineering for the repair project of the guides and sealing frames of the maintenance gates of the Powerhouse No 1 of the Hydroelectric Complex Simon Bolivar.
In 1985 the dam crest was elevated from elevation of 220 masl to 272 masl. This increases the water column in water intakes of Powerhouse I from 40 to 90 m. As the dam ages, seepage occurs through the second-stage concrete of the seal frames. Second-stage concrete needs to be repaired to eliminate leaks and make them able to support the pressure. The difficulty of this work is that there is no gate or mechanism that allows sealing upstream to allow performing the repair works.
The process begins with the design and manufacture of a Submersible Floating Gate (CFS acronym in spanish) whose function is to close the passage of water from the reservoir to the unit's water intake, sealing the entire perimeter of the intake, to drain the water from the interior and have a dry space to repair the guides and sealing frames of the maintenance stop logs. The CFS Underwater Floating Gate is designed to operate at a depth of 90 meters in conditions of high hydrostatic pressure and total darkness. In order to accurately position the CFS on the socket, it is operated from the inside by specialized personnel. For this reason, its functionality, evacuation systems and life support in general, are similar to those of a submarine.
Fapco Hydro built the CFS which is a challenging project that combines metal mechanical construction with submarine technology.
The gate is a monumental structure formed by a hollow hull measuring 20 x 20 x 5.5 m and a 5 m diameter cylinder on top. The total dead weight is 2,000 tons. It was built following strict safety standards for manned submersible vehicles.
Despite its great weight, the gate floats and can be easily maneuvered in water. The gate has ballast and balancing tanks inside which allows to place it at neutral weight (zero weight) and vertical position by entering water. Once in neutral weight, the gate is submerged in a controlled matter to the sealing position in front of the intake.
Once built, the gate was subjected to very strict protocols of immersion tests up to 120 m depths, to verify that it can operate safely and smoothly at the depth of the intakes (90 m).
The gate is available for when it is required to seal an intake and repair its seal frames from the maintenance gates.
This gate allows to seal the water intake, to have a dry space to repair the maintenance sealing frames, which will allow to extend the service life of the generation units of the hydroelectric plant.
see video